Why Choose Our Die Casting Services?
Discover the benefits of our die casting services, where high production efficiency meets unmatched precision and cost-effectiveness. Our advanced techniques ensure consistent quality, reducing waste and saving costs. From initial consultation to final delivery, our streamlined process guarantees timely and reliable results tailored to your needs.
Discover the Key Features of Our Die Casting Solutions
Discover the key features of our die casting solutions designed to meet high-volume production needs. Our solutions boast exceptional durability, the ability to manufacture complex shapes, and superior surface finish, making them ideal for scaling up your production efficiently and economically.
Exceptional Durability
Our die casting solutions provide exceptional durability, ensuring that your parts withstand rigorous use and environmental challenges. This durability translates to longer-lasting products and reduced maintenance costs.
Complex Shape Manufacturing
With our die casting technology, you can easily manufacture complex shapes with high precision. This capability allows for intricate designs and detailed features that are difficult to achieve with other production methods.
Superior Surface Finish
Achieve a superior surface finish with our die casting solutions. Our process ensures smooth, high-quality surfaces that often require little to no post-processing, saving you time and cost in production.
Applications of Die Casting
Discover how our advanced die casting solutions cater to diverse industries, including automotive, electronics, and aerospace. Learn how our features enhance performance and efficiency across various applications.
Automotive Die Casting Applications
Our die casting solutions are integral to the automotive industry, providing lightweight and durable components for vehicles. From engine blocks to transmission cases, our precision die casting ensures high performance and reliability. Explore more about our automotive solutions.
Electronics and Electrical Die Casting
Enhance your electronic devices with our die casting services. We specialize in creating enclosures and heat sinks that offer superior thermal management and electrical insulation. Learn how our solutions can optimize your electronic products.
Aerospace Die Casting Innovations
Our die casting technology meets the stringent demands of the aerospace industry. We produce lightweight, high-strength components that withstand extreme conditions. Discover our contributions to aerospace advancements.
Die Casting for Consumer Products
From household appliances to personal gadgets, our die casting services ensure high-quality and aesthetically pleasing products. We deliver intricate designs with excellent durability. See how we enhance consumer product manufacturing.
Industrial Manufacturing Die Casting
Our die casting solutions support industrial manufacturing with robust and precise components. Whether for machinery or tooling, our services improve efficiency and longevity. Learn more about our industrial applications.
Medical Equipment Die Casting
We provide die casting services for the medical industry, producing components that meet rigorous standards for safety and reliability. Our solutions are ideal for medical devices and equipment. Discover our medical die casting capabilities.
Common Questions About Die Casting
Die casting is a metal casting process where molten metal is injected into a mold cavity under high pressure. The mold cavity is created using two hardened tool steel dies, which are machined into shape and work similarly to an injection mold during the process. This method allows for the mass production of metal parts with high precision and surface finish.
Die casting is ideal for high-volume production due to its ability to produce complex shapes with tight tolerances and smooth surfaces. It offers excellent repeatability, which is essential for large-scale manufacturing. Additionally, die casting is cost-effective for producing thousands of parts, thanks to economies of scale, making it preferable over CNC machining or 3D printing for large quantities.
The most common materials used in die casting include aluminum, zinc, magnesium, and copper. Each material has unique properties that make it suitable for different applications. For instance, aluminum is lightweight and corrosion-resistant, while zinc offers high strength and hardness. The choice of material depends on the specific requirements of the final product.
Die casting is more economical for high-volume production compared to CNC machining and 3D printing. While CNC machining is suitable for low to medium volumes and offers high precision, it becomes costly for large quantities. 3D printing is ideal for prototyping and small batches but isn't cost-effective for mass production. Die casting provides a balance of cost, speed, and quality for large-scale manufacturing.
Die-cast parts are used in various industries, including automotive, aerospace, electronics, and consumer goods. Common applications include engine components, housings, brackets, and enclosures. The process is favored for parts requiring high strength, durability, and intricate designs, making it versatile for numerous industrial applications.
When designing for die casting, consider factors such as draft angles, wall thickness, and rib placement to ensure proper mold filling and part ejection. Uniform wall thickness helps prevent defects, while appropriate draft angles facilitate easy removal from the mold. Incorporating these design principles ensures high-quality, defect-free parts and efficient production.
Yes, die casting can be used for both small and large parts. The process is versatile and can accommodate a wide range of sizes and weights. However, the size of the part may impact the choice of material and the specific die casting method used. For instance, larger parts may require different alloys or specialized equipment to ensure quality and precision.
Lead times for die-cast parts vary depending on the complexity of the design, the size of the production run, and the availability of materials. Generally, the initial tooling and setup can take several weeks, but once the dies are prepared, production runs can be completed relatively quickly. For large-scale production, die casting offers faster turnaround times compared to other manufacturing methods.
What Our Clients Say
John Anderson
The die casting service has been a game-changer for our production line. We needed to scale up to thousands of units, and the efficiency and cost-effectiveness were exactly what we needed. The quality of each part is consistently high, and the turnaround time is impressive.
Emily Roberts
We switched to die casting for our metal parts production and couldn't be happier. The precision and durability of the parts have significantly improved, and we've seen a reduction in production costs. This service has allowed us to meet increasing demand without compromising on quality.
Michael Lee
As a startup, scaling up production was a daunting task. The die casting service provided an economical solution without sacrificing quality. We were able to produce thousands of units efficiently, which was crucial for our market launch. Highly recommended!
Sarah Johnson
Our company needed to ramp up production quickly, and die casting was the perfect solution. The team was professional and delivered high-quality parts on time. This service has been instrumental in helping us meet our production goals and maintain customer satisfaction.
David Martinez
We were initially using CNC machining for our metal parts, but as demand grew, it became unsustainable. Switching to die casting was the best decision we made. The cost savings and production speed have been phenomenal, and the parts are just as precise and reliable.
Lisa Brown
The transition to die casting for our high-volume production needs was seamless. The parts are of exceptional quality, and the process is much more cost-effective than our previous methods. This service has enabled us to scale up efficiently and meet market demands.
Request Your Personalized Quote Now!
Ready to scale up your production? Get a personalized quote tailored to your high-volume manufacturing needs. Whether you require injection molding for plastics or investment casting for metals, our experts are here to help you optimize costs and efficiency. Contact us now to streamline your production process and achieve economies of scale.
Request Your Quote NowLearn More About Die Casting
Discover a selection of insightful articles on die casting to enhance your knowledge and keep you engaged. Learn about the advantages of die casting for high-volume production, understand the economic benefits, and explore detailed comparisons with other manufacturing methods like CNC machining and 3D printing. Stay informed with our expert-curated content, tailored to help you make the best decisions for scaling up your production efficiently.
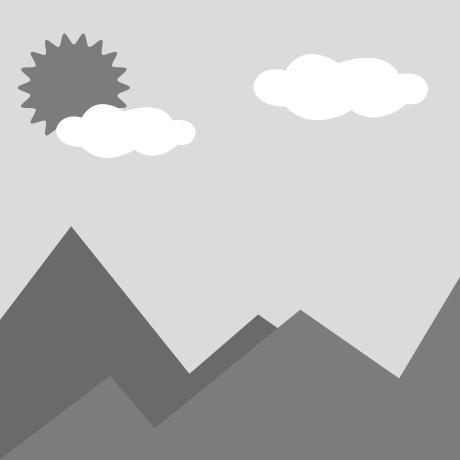
Precision CNC Machining at Yetta
2025-03-05
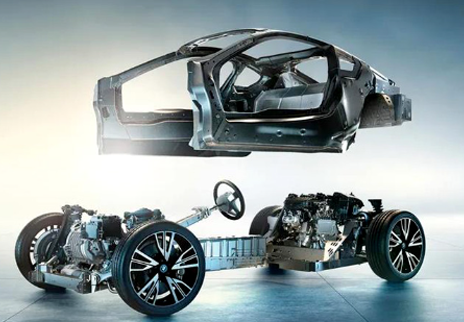
What Is Rapid Prototyping in Automotive?
2024-12-04
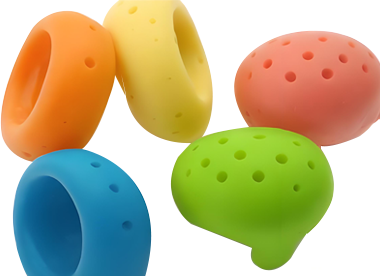
What Are the Most Common Die Cast Materials?
2025-01-17
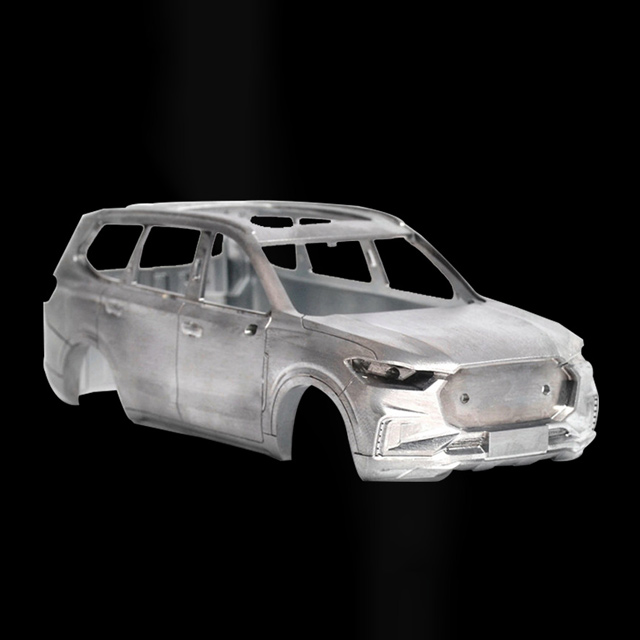
What Are the Steps of Rapid Prototyping?
2024-12-11
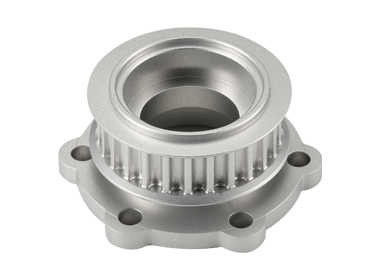
What is a Die Casting Process?
2025-01-15